AkzoNobel Unveils Global Identity for Let's Colour Brands
AMSTERDAM, the Netherlands - AkzoNobel announced an important step in its global Decorative Paints' marketing strategy: a single global brand identity for its retail consumer paint range. The Let's Colour identity includes the brands Dulux, Flexa, Levis, Alba, Coral, Sadolin, Marshall, Astral, Bruguer, Dulux Valentine, Inca, Sadolin and Vivechrom.
The new global brand identity is being rolled out worldwide, starting in Canada, China, India, Southeast Asia and Pacific, and the Netherlands. Other countries and regions will follow during the course of the year, with the new brand identity eventually being deployed in close to 50 key markets. In addition, the AkzoNobel company endorsement will be introduced on the front of packs, as well as on all advertisements, product Web sites and other relevant marketing materials.
Developed through extensive research, the new brand identity is based around a "Flourish" logo, which embodies the Decorative Paints' global Let's Colour campaign. It features a human figure and colorful "Flourish", which will appear on all product packaging for the Let's Colour brands.
Ashland Completes Expansion of Manufacturing Facility in Georgia
WILMINGTON, DE – Ashland Specialty Ingredients, a commercial unit of Ashland Inc., has completed a 13,000-square-foot expansion of its Macon, GA, facility and moved its Nuosept™ biocides production line to the new space. By moving Nuosept biocide production from Leaside, Ontario, to Macon, Ashland has increased production flexibility and efficiency. The production lines are now fully operational.
“With 11 mixing vessels ranging from 75 gallons to 6,000 gallons and every size in between, we can fulfill most any size order, large or small,” said Chris Kollman, Plant Manager. There are 64 tanks on site, including 30 bulk tanks and 19 3,000-5,000-gallon day tanks, which enable Ashland to store finished product until it is shipped and to free up the mills for additional production. The plant runs three shifts covering 24 hours per day Monday through Friday, and can run Saturday if necessary.
“Biocides volume comes in surges,” added Russell Jerusik, Biocides Product Manager, Ashland Specialty Ingredients. “When we need to produce large volumes, we can use the full plant staff. Conversely, we also have the flexibility to produce very quickly with very little lead time.” That same flexibility, Jerusik said, enables Ashland to produce different blended products and volumes simultaneously and efficiently.
The plant also has a pilot-sized mini-mill to produce experimental batches. The mini-mill helps Ashland innovate and develop new biocides that can then be scaled up to production volumes. The mini-mill also enables technicians to look at variations in the manufacturing process and troubleshoot customers’ production problems.
Camfil APC Expands Corporate Headquarters
JONESBORO, AR - Camfil Air Pollution Control (APC) has expanded its corporate headquarters in Jonesboro, AR, with the recent opening of a 13,600-square-foot office facility for sales and administrative staff. The facility includes open-plan and private offices for 85 employees and a training center to be used for customer and internal training and educational programs. Construction of the new office building has also freed up additional production space in the Jonesboro manufacturing plant.
The corporate headquarters expansion is the latest step in a worldwide global development program by Camfil APC. The recent acquisition of Handte, a German manufacturer of dust collectors, mist collectors and wet scrubbers that strategically complement the Farr Gold Series® cartridge dust collection line, has nearly doubled the size of the company.
Camfil APC is a leading global manufacturer of dust collection equipment and is part of Camfil, a leader in air filters and clean air solutions.
Michelman Unveils New Brand Identity
CINCINNATI – Michelman introduced its new brand identity at the American Coatings Show in Atlanta. The company has evolved into a proactive, forward-thinking company, able to anticipate customer and industry challenges and needs, and deliver innovative and optimal solutions anywhere in the world, quickly and efficiently. The new identity better reflects Michelman’s leadership position in the coatings, composites, and printing and packaging market sectors it currently serves.
Over the past six years, Michelman has evolved into an international force in each of the markets it serves. The company has increased its technological capabilities, enhanced its global regulatory compliance capabilities, made a number of key acquisitions in the United States and Europe, and entered the Japanese market through a joint venture. It has expanded its global footprint with new facilities in Germany, China and India and has added a state-of-the-art R&D facility in Windhof, Luxembourg, with another scheduled to open at the company’s Cincinnati headquarters in the summer of 2014. These facilities are in addition to Michelman’s long-established production facilities in the United States, Singapore and Belgium.
According to Bob Poletti, Chief Marketing and Corporate Development Officer at Michelman, “Michelman is not the same company it was five or six years ago. In the economic downturn of 2008, when most companies were pulling back investment, we continued to push forward. We invested strategically in key areas of the world and in core or complementary industry segments. We’ve added many talented associates who have helped position Michelman as thought leaders and as a company who is able to think ahead to what will be the ‘next’ solution. All of these investments and more have helped us reach the point where we can assure customers we will provide forward-thinking, proactive, environmentally friendly solutions.”
The clean new brand mark symbolizes Michelman’s evolution and acts as a signal to customers of Michelman’s commitment to forward-looking, agile solution development.
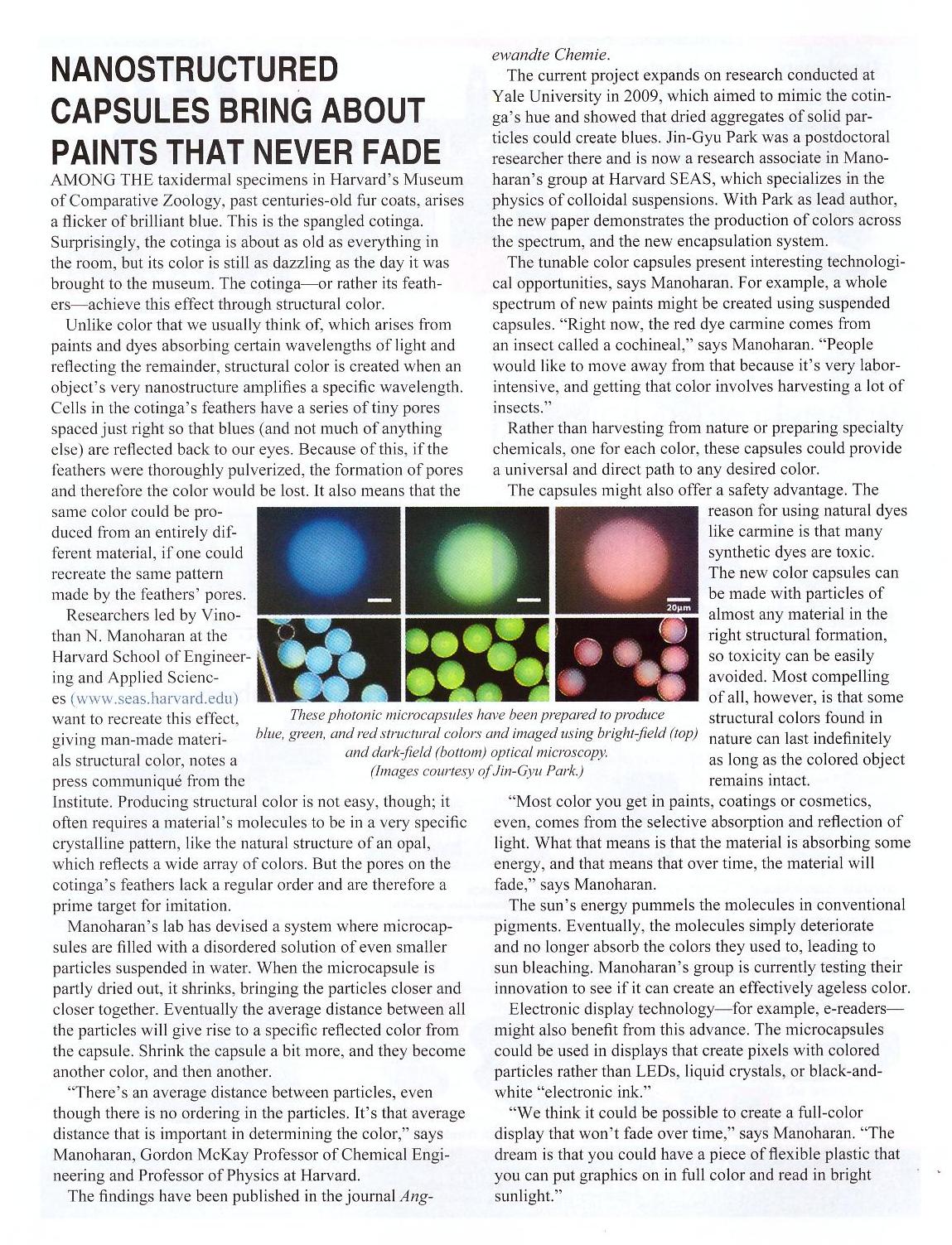
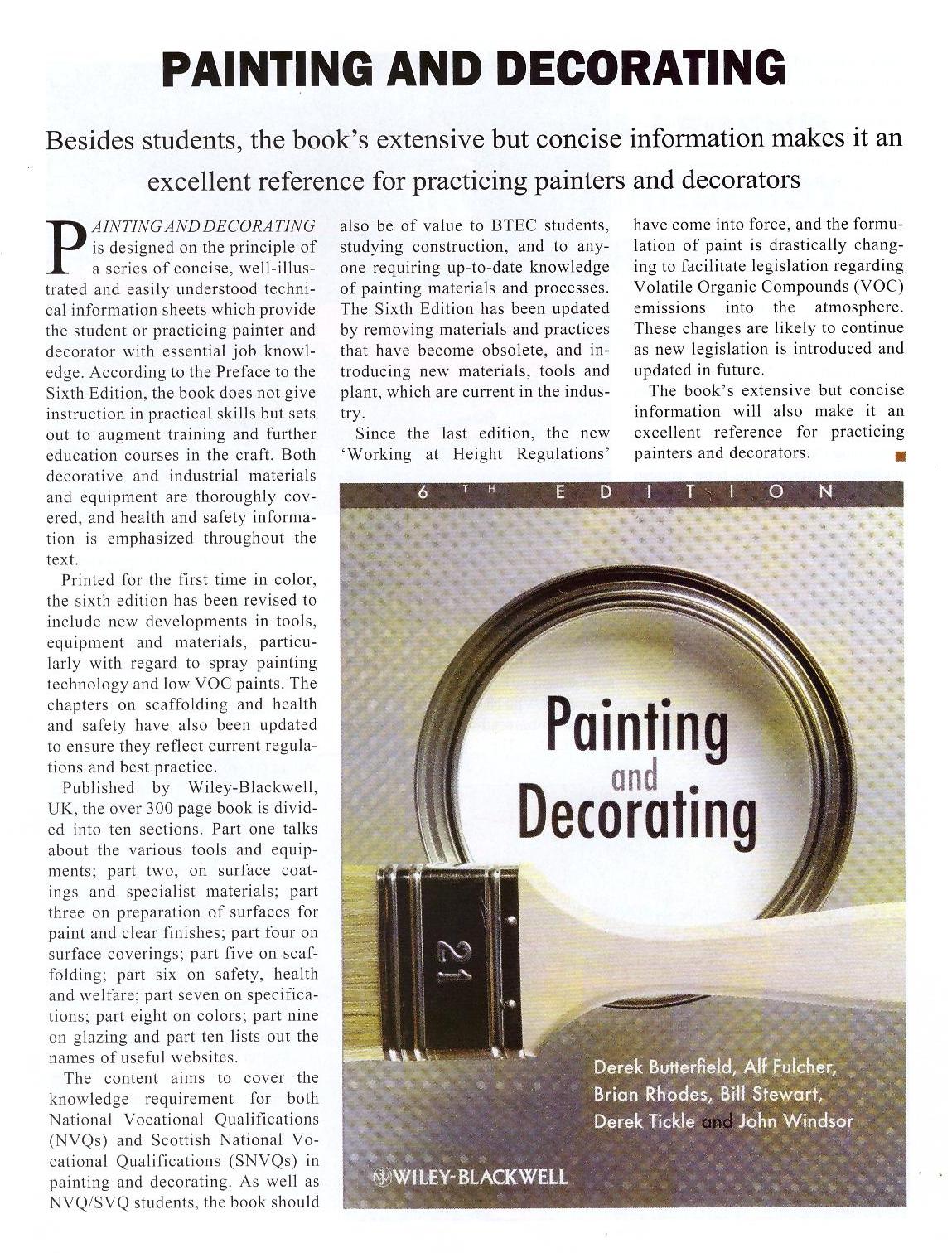
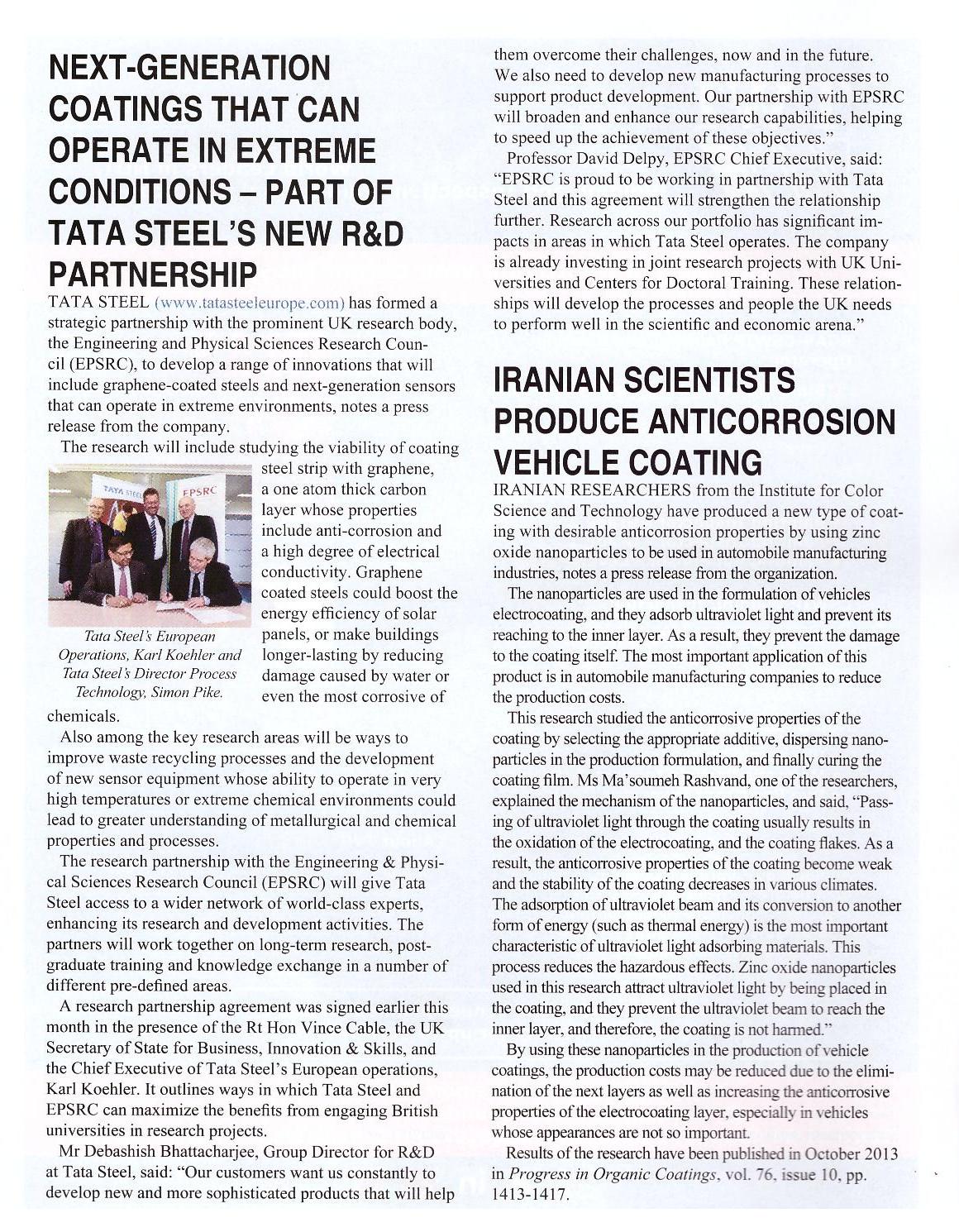
SSPC 2014 Conference and Exhibition in Florida
I was at the SSPC 2014 Conference and Exhibition in Florida, USA a couple of weeks ago. One of the things I learnt there was that the University of Akron, USA, had started a bachelor’s degree program ‘Corrosion and Reliability Engineering’ a couple of years ago. It was the first of its kind in the USA and it’s a course that has been doing well.
The program takes a unique approach to an old and expensive problem – rust, practically everywhere. It was the private industry that had clamored for this degree. Industry isn’t kidding. The demand exists. Companies find themselves training new people to deal with corrosion. Why not have universities perform the preparation, patiently, deliberately and fully.
Corrosion is no small problem. The US Government’s Accountability Office puts the annual cost to the economy at US$400 billion. Corrosion’s estimated annual impact worldwide is said to be US$2.5 trillion.
The thinking is that the savings could be as high as 30 percent if companies and agencies manage well their corrosion, prolonging the life of bridges, pipelines and the likes, liberating tens of billions of dollars for other investments.
The other day, at the 50th AGM of the Indian Paint Association (IPA) Mr Abhijit Roy, MD and CEO of Berger Paints India, said that the paint industry in India is in dire need of skilled painters. The lack of skilled painters is a matter of great concern. The paint industry is a promising industry that can generate employment to 15 lakh persons, he said. The IPA has taken steps to set up a body to give out certificates to trained painters as part of the initiative to bridge the gap.
My dream is that every State in India should have a proper center where education on corrosion mitigation is imparted. It could be private institutes or universities, it doesn’t matter. After all, rust can work to their advantage!
The Importance of Characterizing the Force Needed to Initiate Material Flow
Introduction
The phenomenon known as creep characterizes material flow behavior. This applies to a number of liquids, semi-solids such as gels and lotions that continue to move slightly even after being placed on the skin. The research and development team need to understand how much force is required to initiate material flow, how long material movement will continue once flow has commenced and the potential deformation or displacement of the material with reference to its initial position.
Using Stress Rheometers for Characterizing Force
This behavior can be characterized by controlled stress rheometers. Figure 1 shows the cone and plate model that can work with a very small sample size, normally less than 1mL in order to make the measurement. To simulate body temperature, the substance is placed on a temperature controlled plate at 98.6°F. The cone spindle and the substance are brought into contact, which spreads out filling the gap between plate and spindle. The sandwiched material is ready for evaluation at test temperature.
Firstly it is important to determine how much force will cause the material to flow, which is known as the yield stress. Controlled stress rheometers are more beneficial over other instruments for making this kind of measurement. Increasing torque is slowly applied to the cone spindle until a very slight amount of rotational movement is detected.
It is possible to find out with very high precision when the spindle changes from its stationary position and first begins to rotate using an optical encoder. Initially the movement will be because of elastic stretch of the sample structure and hence completely recoverable. At a specific stress, the onset of flow for the substance is established clearly without destroying or compromising the structure of the material before that moment in time.
The graph of yield stress measurement for two different materials measured by a controlled stress rheometer is shown in Figure 2. The x-axis is the controlled stress applied to the material by the rheometer while the y-axis is the shear rate applied to the material as measured by the instrument.
After yield occurs, the question is whether flow movement will continue, particularly if the force applied to the material reduces or is removed altogether. Creep is the term used in order to characterize continuing deformation at a slow rate of movement after yield. The controlled stress rheometer is qualified to render this measurement as it can continue to apply the low force to the material simulating the real-life situation, such as gravity causing a medicinal lotion to sag after application. The graph of creep behavior for the same two materials is shown in Figure 3.
Brookfield RST Controlled Stress Rheometer with Cone/Plate Geometry
Graph of Yield Stress Behavior for Two Different Materials
Graph of Creep Behavior for Two Different Materials
Thr y-axis is the angle of rotation for the cone spindle meassured by the instrument vs. the x-axis which is simply the elapsed time that the material is exposed to the controlled stress. When stress is removed, recovery needs to occur, which is the ability of the material to return to its original position after being sheared.
The graph for the same two materials in recovery mode is shown in Figure 4. There is a sudden reduction in the angle of rotation for the cone spindle that is it physically rotates the cone spindle in the opposite direction as the material’s internal structure exerts a backwards movement force on the spindle.
Graph of Creep Behavior for Two Different Materials
For materials that require to hold or preserve structure for fulfilling their purpose, perhaps synthetic materials such as putties used to fill deteriorated bone, this resistance to movement is important. Consequently, recovery behavior after placement implies the material will return to its original shape.
Conclusion
In the medical and pharmaceutical industries, companies turn to controlled stress rheometers in order to measure and better understand these properties and modes of behavior for yield stress, creep and recovery. In case one has used a viscometer to make flow measurements it is not likely that one has measured these properties with any effectiveness. This is probably the right time to move forward and study the larger world of rheology that encompasses aspects of flow that are more subtle, but very essential for many of the products to succeed.